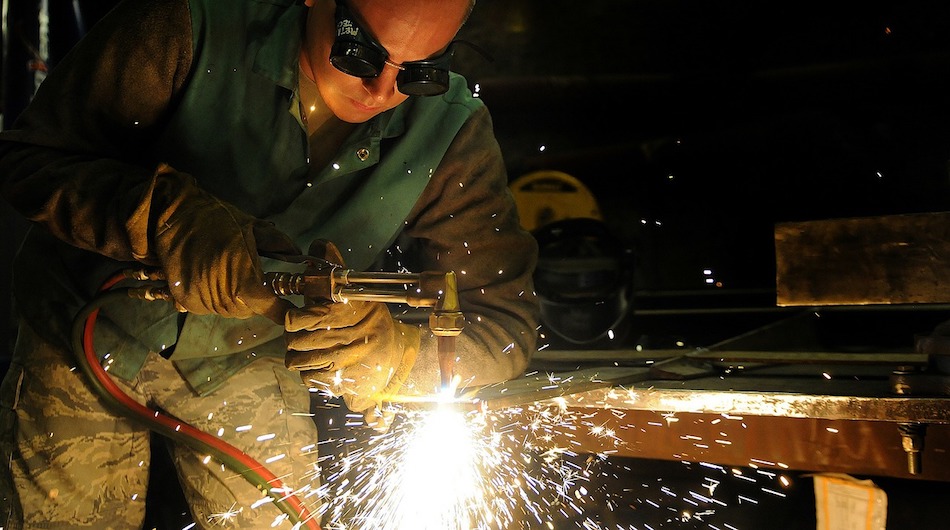
Image credit: Pixabay.
The Internet of Things (IoT) is synonymous with smart home applications like controlling your lights and appliances with a phone. But IoT’s real potential isn’t in phone notifications about a completed spin cycle — it’s in industry.
According to a study by Accenture, conservative estimates place spending on industrial IoT (or IIoT) worldwide at US$20 billion in 2012, with spending expected to reach US$500 billion by 2020.
To study the growth of IIoT, look to manufacturing in Indonesia. A strong economic force in Southeast Asia, the country’s manufacturing sector contributed 20.4 percent of GDP in Q3 2016, with data by the OECD suggesting that Indonesia has one of the highest industrial production growth in the world.
The sector capacity is running at approximately 30 to 35 percent below potential, according to GE statistics. The opportunities for disruption are immense.
Here are the benefits IIoT machinery could bring to Indonesia’s manufacturing sector:
Navigating geographic distances
Indonesia has a large land mass, and as a result, geographic distances between facilities may impede collaboration and resource-sharing. To overcome these distances, digital-assisted industrial tools can maintain a record of work, ensuring that each worker has a transparent understanding of work done elsewhere and the data needed to get their operations in check.
Maintenance and repair procedures are also stored in a database so that every facility can cope with hardware issues. If need be, secure cloud-based communications allow specialists and engineers to collaborate on a problem, enabling more better teamwork and decision-making even from remote locations.
Talking machine parts
At the GE Minds + Machine 2016 conference, GE presented the use of digital twin technology – which uses sensors from real-world objects like industrial equipment to create a digital model – in servicing a steam turbine. With an AR headset and voice recognition software, an engineer can detect trouble spots within a turbine, and be guided through complex procedures of assembly, maintenance, and repair.
Digital twins also communicate with each other, like different parts of a jet engine consulting each other on unexpected conditions and compare notes. To make things more interesting, digital twins would have access to market information, current demand and supply conditions, and market pricing. Based on this information, the digital twin can communicate with the human operator to propose strategies, such as the rates of running gas turbines or avoiding overworking a part because of higher maintenance costs.
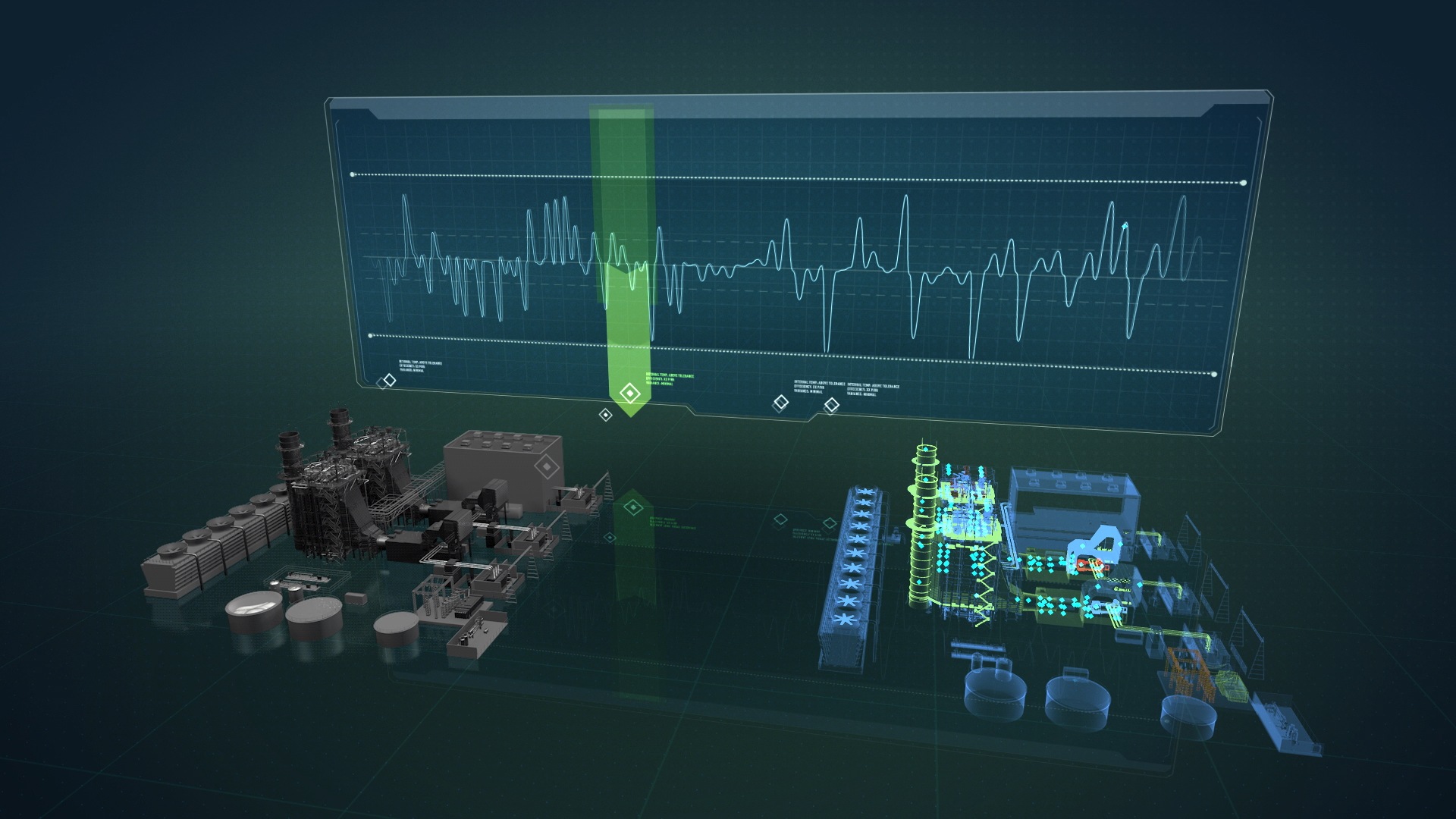
A “digital twin” of an asset providing continuous feedback on performance. Image credit: GE Reports.
Eye on the factory
IIoT can also enhance economies of scale. “Digital Thread,” a software developed by GE’s Brilliant Factories, is essentially a system of electronic sensors and software analytics that connect every element of the factory floor, including workers and machinery. Each factory is also linked to the full supply chain, to ensure that delays in both production and deliveries can be tracked.
With data such as cost and process consequences, factories can adapt effectively to market conditions or disruptions. If an additive manufacturing facility is disrupted by machine failure, the system can provide solutions.
The road ahead
The benefits of IIoT are easy to showcase, and advanced factories like that in Geek+ and Foxconn shows that the technology is ready and waiting to be adopted. But before Indonesia can take on that next level of manufacturing, GE cautions that the country has to place some key enabling conditions.
Infrastructure, such as transportation, energy, healthcare, and communications, has to be in place to make full use of technology. Workers need to become familiar with technology or have opportunities for retraining or on-the-job learning.
The business environment also needs to improve. Indonesia ranked 91st out of 190 countries in the 2016 World Bank’s Ease of Doing Business report; it ranked a poor 151st for the ease of starting a new business.
The manufacturing sector stands to gain by shifting from a centralized, traditional structure to a more diversified group of smaller, agile, and technologically advanced firms.
The Indonesian government would need to work closely with the private sector to ensure that the conditions for competitiveness are in place.
Only then can the industrial internet truly transform Indonesia.
If you’d like to learn more about how advanced technologies will be shaping Indonesia’s future, download GE’s whitepaper on the Future of Work in Indonesia here. Check out more stories about digital industrial written in Bahasa Indonesia and English.
This post Forget smart homes — industrial IoT is what Indonesia should focus on appeared first on Tech in Asia.
from Tech in Asia https://www.techinasia.com/iiot-indonesia
via IFTTT
No comments:
Post a Comment